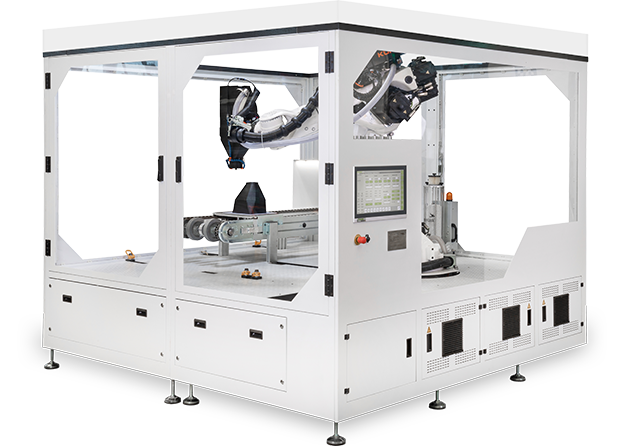
Overview
Additive Manufacturing – economically minded
SpaceA technology is based on the layer-by-layer deposition of one molten thermoplastic. A solid component can be built up by solidifying this melt strand.
Yizumi’s SpaceA technology is based on 4 principles for economical use:
- Use of a screw extruder
- Use of a 6-axis positioning system
- Use of a high plant modularity
- Use of an industry standard control system
First, the material which will be processed is pretreated in a dryer (1). This dryer is included in all standard systems. The material is fed from the dryer to the extruder (2).
The extruder is a compact single-screw extruder, weighing only 6.5 kg. There the pellets are plasticized and discharged in a defined manner. The final component can then be produced on the construction platform (3) by a relative movement of the positioning system (4).
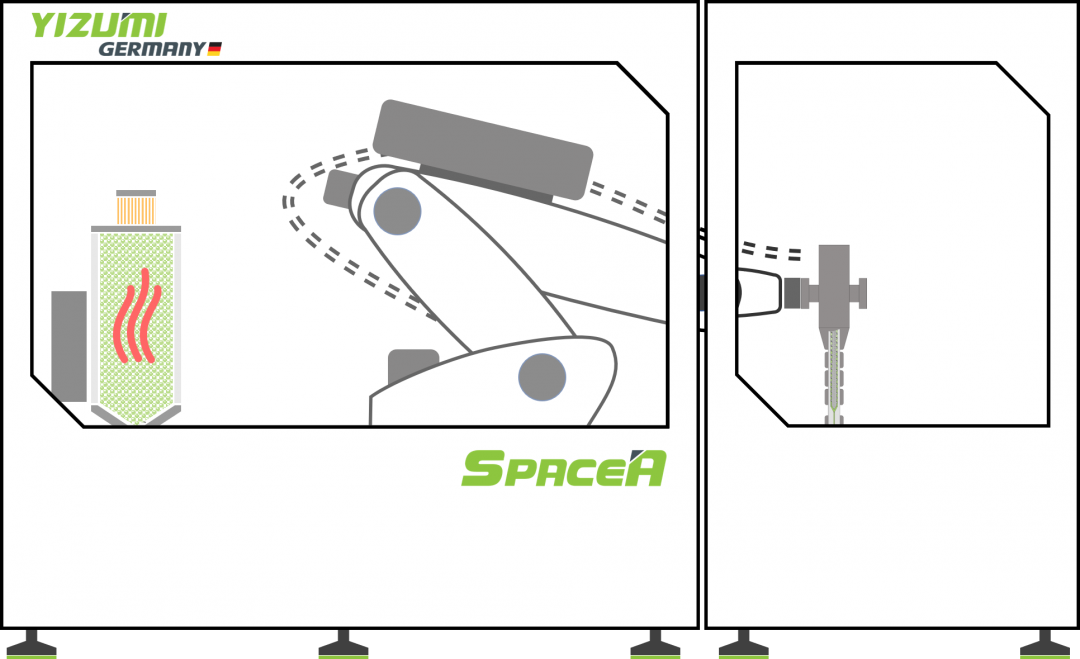
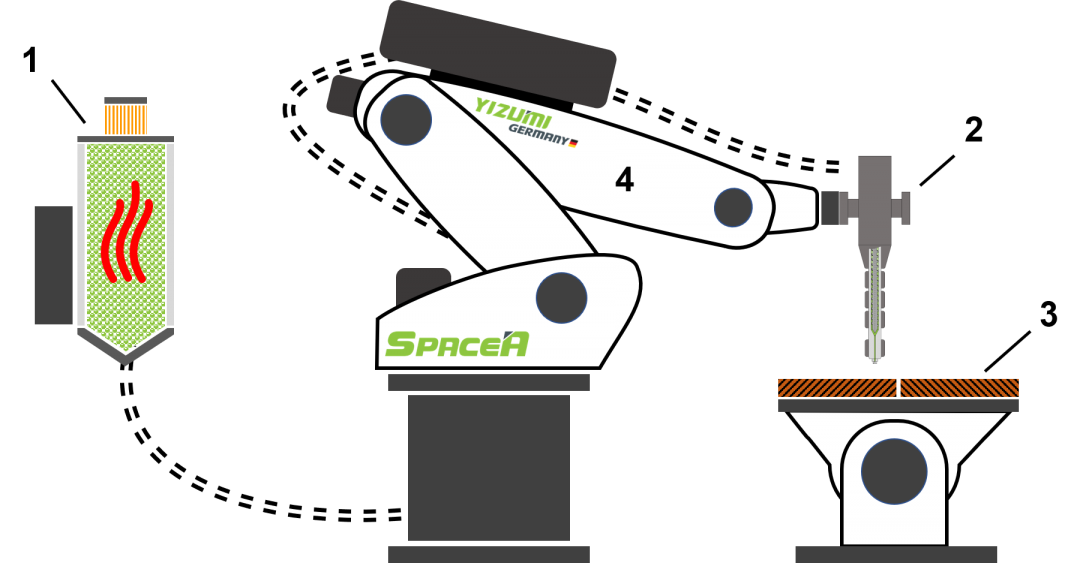
Additive Manufacturing
Your Benefits on one Sight
Automatability
Scalable in line combineable with prototype methods. Combination of additive and subtractive manufacturing processes.
Productivity
28 times faster than conventional FLM processes
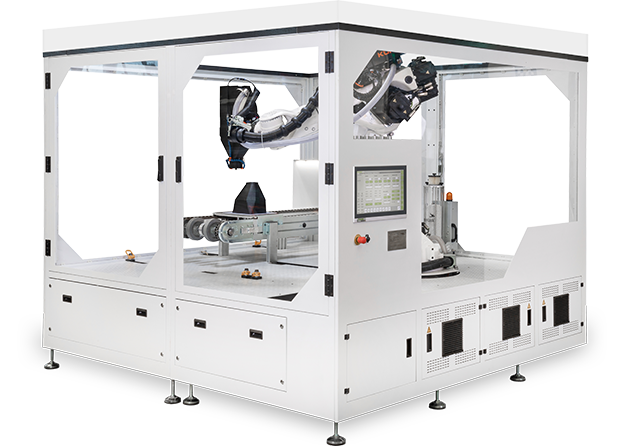
Scalability
The SpaceA product family is flexibly scalable in size and material discharge.
Material variety
Any thermoplastic granulate can be used.
Additive Manufacturing
PRODUCTS VARIANTS – SpaceA
Extract from our assortment
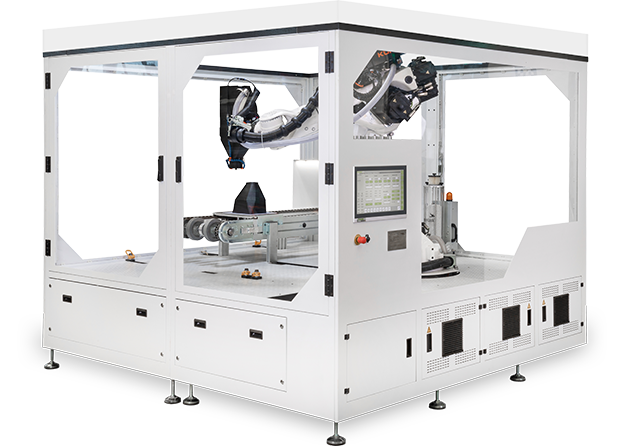
SpaceA S-Line
Fixed Platen
Standard All in One 3D printer available in sizes
0.9 to 2.5 meter KUKA arm available.
Includes:
Material dryer, material conveyor, screw extruder, industrial robot, controller and software package
The compact design and the ability to set up the S-Line products flexibly anywhere make this series unique. Moved into place with a pallet truck, you can get started straight away with this plug-and-play solution.
– No need to fix the system in place
– No additional accessories required
– No additional software required.
Thanks to the modular design, changes can also be made at a later stage, e.g. changing the extruder from approx. 3.5 kg/h to 10 kg/h or integrating a conveyor belt to automate the system for a series process.
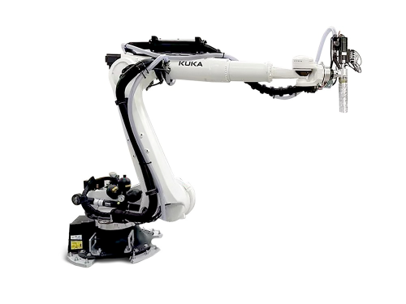
SpaceA B-Line
Fixed Platen
The big all-inclusive solution. From 1.6 to 3.9 meters Kuka arm, our popular Beckhoff-based HMI and from currently 3 extruder types with up to 20 kg/h output and different tables you can choose your Big Printer.
Additive manufacturing can be as easy as injection molding – just fill the dryer with pellets and get started.
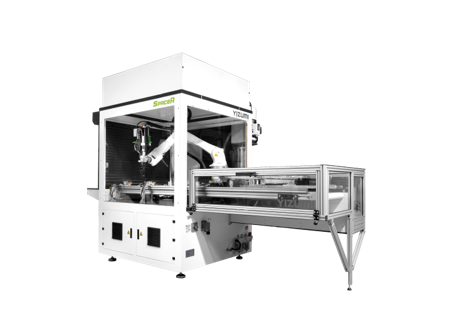
SpaceA C-Line
Piece Carrier System
With our in-house designers and technicians, we are able to work with you on virtually unlimited projects. A product from the S-Line or B-Line series serves as the basis for a C-Line system.
Some examples: Combination of printing and milling, camera monitoring, sensor integration, plate separation and feeding for the production of hybrid components, high degree of automation for industrial production and much more. With the SpaceA C-Line, you also get an all-in-one solution.
FAQ
Questions & Answers
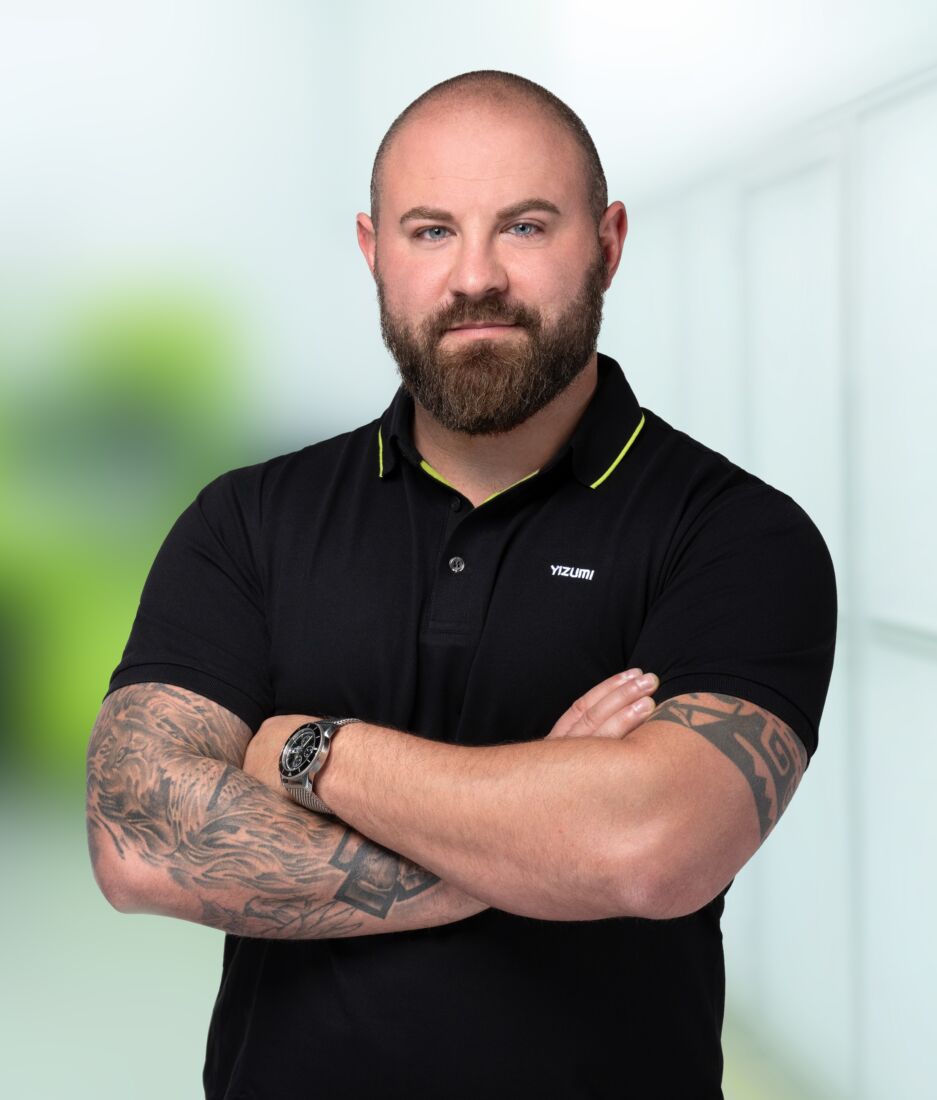
Sandro Redina
Global Sales & Marketing Manager
Additive Manufacturing
Phone: +49 152 26 25 1942
s.redina@yizumi-germany.de
1. What is the main problem with today's competing technologies for additive manufacturing?
Most machine suppliers for AM-machines expect machine costs and material costs to be too high. If we want to use additive manufacturing in real production, we have to benchmark ourselves with injection moulding technology and for this we really have to reduce material costs to the standard granulate price and machine costs far below the cost of injection moulds.
2. And this is Yizumi's approach?
Yes, we want to use injection moulding as a benchmark and try to offer our customers a real benefit in using our AM technology. And our SpaceA systems can process standard granules so that PMMA or highly filled materials are no problem for us. This allows us to reduce part costs for the first time. In addition, we have developed a truly cost-saving machine and extruder technology to reduce machine costs. Both tracks lead to low part costs and so we can offer an attractive technology for small batch sizes and medium batch sizes up to 10,000 parts.
3. What machines does Yizumi offer?
At the moment we have three standard product lines. First the extruder extension packages. Here we only offer the extruder with control and material supply. This package is an intelligent solution for all customers who already have an automation cell with a six-axis robot system. Secondly, we have a small machine series and thirdly a large machine service. In all our product lines we offer our customers additional full flexibility. This allows us to easily adapt the standard packages to their needs.
4. How far can the automation approach be scaled?
The automation approach of the SpaceA product family, like any general automation approach, is completely scalable. It is based on our innovative extruder, which can be handled via 6-axis positioning systems. Combinations of different production technologies such as milling, injection moulding, thixomolding, die casting or thermoforming can be implemented. Finally, the right combination of the various state-of-the-art technologies is crucial in order to produce a cost-effective component that meets the requirements.
5. And could you already present automated production lines?
Yes, twice. At the last K 2019 in Düsseldorf. Since the K-Show is production-oriented, we showed in two cases the integration of a SpaceA AM system into a fully automated injection molding production cell. This enabled us to reduce the complexity of injection molding. This approach saves a lot of costs in both injection molding machine technology and injection molding tool technology. To give the first example at the Yizumi booth, we produced a strong rib structure in cycle time on our Yizumi engine cover. This way we have an optimized material usage. Strong carbon fiber reinforced material for the rib structure and slightly glass fiber reinforced material for the cover itself. Secondly, we applied a TPE anti-slip structure to a Raspberry Pie housing on the IKV booth. So we were able to show very well that we can meet the injection molding cycle time and are able to handle complex automation systems.
Request