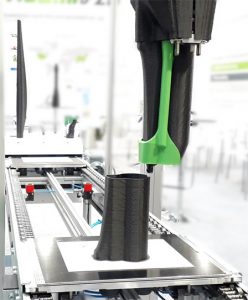
Schneckenextruder mit 16 mm Durchmesser für Standardgranulate
Die Additive Fertigung liegt im Trend und hat sich längst aus der Nische der Prototypenfertigung hin zu einem Produktionserfahren in der Kunststofftechnologie etabliert. Die Yizumi Germany GmbH, Aachener Tochterunternehmen des Urformmaschinenbauers Yizumi Ltd. aus China, der neben Spritzgießmaschinen auch Anlagen zum 3D-Druck herstellt, hat unter der Leitung von Nicolai Lammert eine neue Baureihe namens „SpaceA“ entwickelt.
SpaceA ist eine auf Schneckenextrusion basierende additive Fertigungstechnologie (SEAM) mit einem hybriden Fertigungsansatz, erläutert Lammert, der Leiter Additive Verfahren bei Yizumi Germany. Die neue, robotergeführte Freiformtechnologie, ermöglicht es demnach, auf der Basis von Standardthermoplasten in Granulatform und Blends aus Materialkombinationen mit und ohne Füllstoffen, Formteile mit Dimensionen von 1 cm bis über 200 cm herzustellen. Die Herstellungszeiten für Formteile mit diesem System liegen den Angaben zufolge – je nach Anwendung – meist zwischen 30 und 60 Minuten. Damit wären in der Praxis Serienproduktionen von 3.000 bis 6.000 Teilen pro Jahr auf einer einzigen Anlage möglich, die zudem laut Anbieter wegen der geringen Investitionskosten hochwirtschaftlich seien. Yizumi Germany bietet das System SpaceA in mehreren Raumgrößen und Austragsleistungen an, was eine optimale Anpassung an das individuelle Kundenportfolio ermöglichen soll.
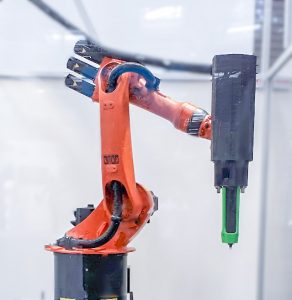
Das eigentliche Prinzip des Systems wurde im Jahr 2015 am IKV (Institut für Gesamtsystem mit Extrusionseinheit an 6-achsigem Industrieroboter
Kunststoffverarbeitung) der RWTH Aachen entwickelt und seit Sommer 2018 bei der Yizumi Germany GmbH in Aachen weiterentwickelt, die dafür eine Partnerschaft mit dem IKV eingegangen ist. Das Verfahren dieser neuen Anlagenserie zur additiven Fertigung wurde letztes Jahr auch bereits auf der Fakuma und auf der Formnext präsentiert. Als Vorteile im Vergleich zu den bereits am Markt etablierten additiven Fertigungsverfahren, wie SLS (Selektives Lasersintern), FDM (Fused Deposition Modeling) oder anderen Verfahren des freien Formens ohne Formwerkzeug nennt das Unternehmen die folgenden Eigenschaften:
- Alle thermoplastischen Standardgranulate ließen sich damit verarbeiten, so auch beispielsweise mit Glas- oder Carbonfasern sowie mit Mineralien hochgefüllte Compounds.
- Eine hohe Schererwärmung im Schneckenextruder erlaube eine produktangepasste Skalierung der Austragsleistung zur konkurrenzfähigen Serienfertigung,
- Es bestehe die Möglichkeit zur Einbringung von Einlegeteilen,
- Hohe Oberflächenqualitäten seien mittels zusätzlicher, in die Hybridzelle integrierbarer, subtraktiver Verfahren (Fräsen, Schleifen) erzielbar,
- Der Einsatz einer modularen Plattformstrategie erlaube die Reduktion von Anlagenkosten.
Die SpaceA Produktfamilie ist modular aufgebaut, so dass der Schneckenextruder mit Fräsern, Greifern, Granulat Trocknern usw. zu einer Hybridzelle erweiterbar ist. Durch diese Modularität lässt sich das System problemlos in bestehende Produktionsketten integrieren, um z.B. Spritzgussteile zu funktionalisieren. Auf diesem Weg lassen sich Dichtungselemente oder auch Verstärkungsstrukturen auf ein Bauteil aufbringen, so dass eine 2K-Spritzgießmaschine sowie eine zweite Kavität im Werkzeug überflüssig werden; zudem kann die funktionale Ergänzung hier von Bauteil zu Bauteil individuell variiert werden.